RG Group - Derby Road, Nottingham
- Alice Sheil - PR Media
- Mar 2, 2023
- 2 min read
RG Group awarded this large project to Stephenson to construct 5 blocks ranging in sizes from 3 to 6 storeys. The blocks are cast in-situ reinforced concrete frames utilising flat slab construction.
Other scope of works consist of groundworks, drainage, reinforced concrete foundations, reinforced concrete columns, reinforced concrete walls and upstands, reinforced concrete stairs and reinforced concrete slabs. The frame consists of 30 suspended rein forced concrete flat slabs with an area of 23,250m², 6 lift cores and 8 stair cores. The groundworks consist of over 200 various sized reinforced concrete pile caps associated with reinforced concrete beams and the drainage works of 95 manholes with pipe lines between them.

Derby Road is a mixed use scheme that will deliver high quality, purpose built student accommodation adjacent to the University of Nottingham's Jubilee campus. The development retains a car showroom garage on Triumph Road and demolishes remaining buildings to accommodate the blocks which provide 700 student beds.
The Project Team
Sorin Duciuc - Contract Manager at Stephenson
Kumaran Vijay - Project Manager at Stephenson
Ovidiu Velea, Daljit Rai, Lee Morris and Viorel Hostiuc - Project Managers at Stephenson
Rory Keane, Evan Denscombe and Theepan Shan - Engineers at Stephenson
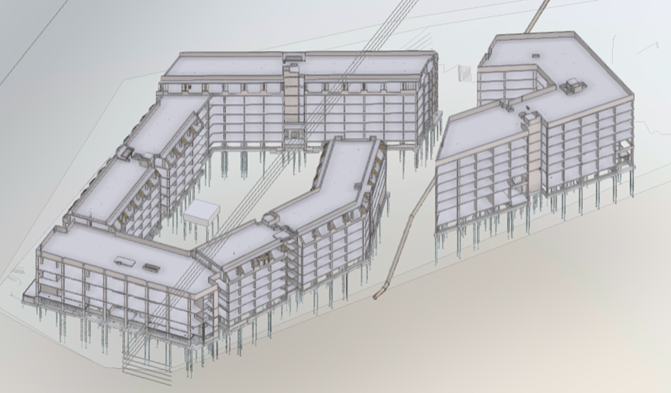
Methodology
Derby Road is located within a flood zone and as such, has been engineered to be predominately above any overland flows. This has been successfully completed with the introduction of a raised, suspended ground floor which is 1.8m from ground level.
Cemex was chosen as the supplier of ready-mix concrete throughout the entire project and supplied over 8,200m³ by the end. Concrete mobile pump, static pump and tower crane lifetable concrete skips were all used as methods to pour the concrete.
RMD Kiwkform supplied the formwork and falsework and required temporary works designs for the build. RMD Airodek and Alshore where used for the slab construction. The ease of instillation in comparison to other traditional options was deemed best suited for this project as it enabled the team to quickly strike and recycle equipment which drastically reduced the volume of kit required.
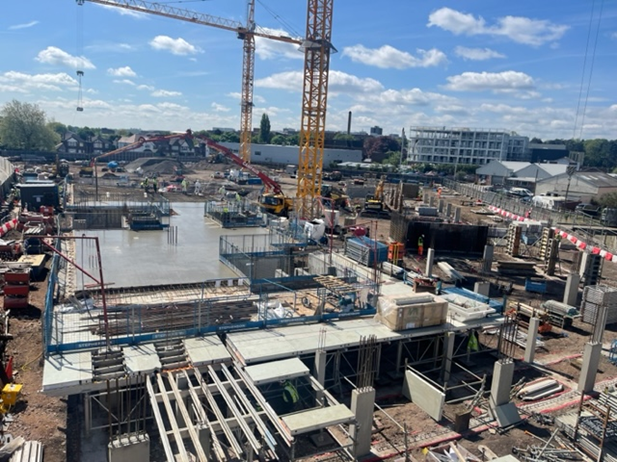
Doka Framex & Plusform ABS shutters were chosen for the vertical elements. The column profile being replicated on all floors helped with the speed of assembly of the shutters from floor to floor. The Plusform ABS shutters required little interaction with the tower crane also assisting with the speed of the build. By utilising both these systems, we were able to eliminate and reduce the use of plywood and crane lifts and ease manual handling across site.
Flexi permanent formwork was installed for the stair construction. This method was employed as the stair design had not been fully developed so enabled the core construction to progress ahead without interruption. The stairs were installed once the design was completed and the speed of installation related to this product mitigated any time lost.
K-Guard was fitted for the edge protection system. Due to it's ease of instillation, flexibility and our teams familiarity, it naturally presented itself as the most viable option.
Cantidek platforms were repositioned at various locations around the reinforced concrete frame to allow quick distribution of materials and equipment. This also prevented any unnecessary double handling of kit therefore reducing the hook time requirements on the crane.
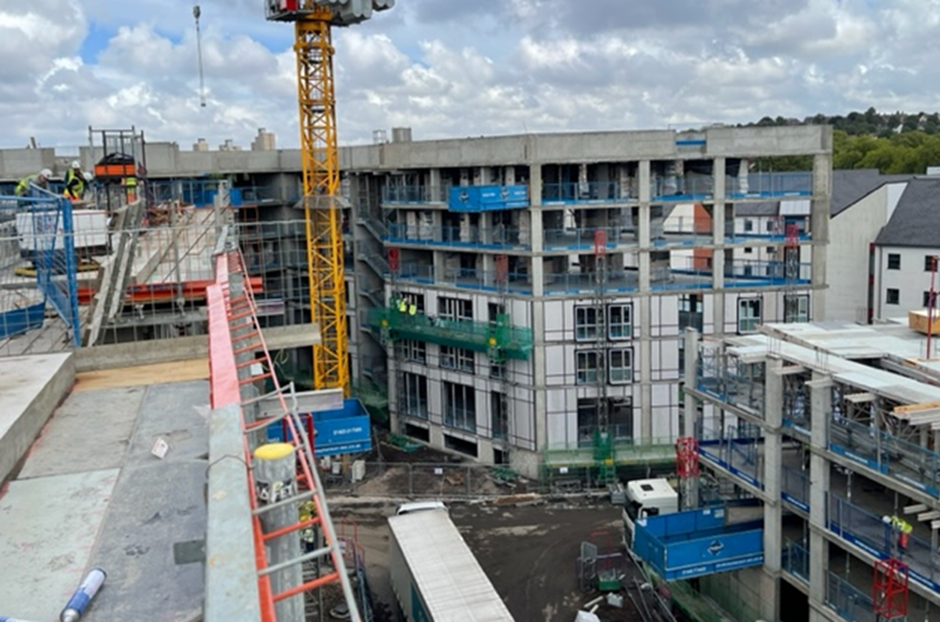
Commentaires