Kier - St Sidwell's Point, Exeter
- chacker23
- Nov 3, 2021
- 4 min read
St Sidwells Point is the UK’s first ever Passivhaus Standard ultra-low carbon Leisure Centre with anticipated savings of 70% on annual running costs.
Kier were appointed by Exeter City Council through the Southern Construction Framework (SCF) to deliver the new city centre leisure centre to replace the existing building.

Kier started work in January 2019 with a 2 year programme on site.
The new facilities include;
Main swimming pool & learner pool with moveable floors
Confidence water pool
100 seat spectator seated area
Café to seat 50
150 station fitness gym and two fitness studios
Health suite and spa facility
Children’s soft play areas on multiple levels
The Project Team
Client: PHT Patron Exeter City Council
Lead Architect: Space and Place Architects
Envelope Architect & Passivhaus Designer: PHT member Gale & Snowden
Project manager: Randall Simmonds
Main Contractor: Kier Construction Western and Wales
Engineer: Arup
Leisure Consultant: Continuum
Certifier: Passivhaus Institute (PHI)

Located on the site of the old Exeter Bus Station the project included a complex multi-level tiered structure within a typically restricted city centre site providing limited off-load, storage and pre-fabrication spaces.
Stephenson started work on site in April 2019 for a 38 week main works programme with a scope of works to deliver “The RC Frame and RC Site works to the first Passivhaus Leisure
Centre in the UK with 3nr Pools and extensive leisure centre facilities”

Key Facts & Figures
Columns; 280 Nr
Walls; 7,570m2
Soffits; 3,800m2
Total Concrete; 11,940m3
Total Reinforcement; 780 tonnes
Shear couplers; 2000 Nr
Introduction
Designed by Space & Place Architects and Engineered by Arup the site topography and design form with its’ unique combination of levels, curves and material interfaces naturally dictated the prevailing sequence of the primary operations with the tiers being constructed in turn from the lower levels which contained the complex structures associated with the pools.
Complexity
As mentioned and evidenced by the CGI and photographs the building form is unique and presented several challenges to the normal planning and execution processes of a traditional RC Frame.
In certain areas of the substructures where traditional temporary works would be used to support retaining walls for backfill operations the profile of the walls was altered to add discreet buttresses and make them self-supporting which allowed progression of the works in front of the wall unencumbered by props.
The superstructure design included a number of complex and highly individual interfaces and forms including a chamfered expanding core, extensive curved beams, multi-chamfered arises to walls and slabs within the pool and plant undercrofts and connections to both complex steel and Glulam structures providing hybrid structural solutions.
One particular example was the main supporting column for the roof between the pools which was 9m in height and circular with 2 corbels in opposite directions with bolt clusters cast into each corbel. The column went from circular to square and back to circular with further bolt clusters cast into the top of the column.
In key areas the access, construction techniques and temporary works required elemental planning and precision and strict adherence to the agreed methodology to achieve the safety, quality and programme objectives.
The main core was advanced using an RMD jumpform system to reduce the impact to the critical path of the project.
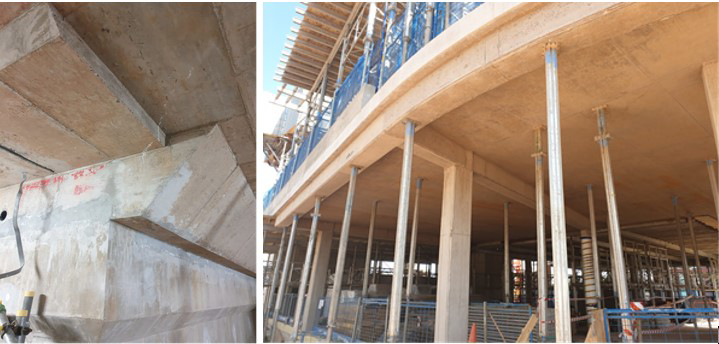
Quality and Workmanship
The project included a number of exposed concrete finishes to columns, walls and soffits which when added to the complexity of the structure added further layers of difficulty.
RAPIDOBAT® Cretcon HD was selected for the circular columns which made it possible to achieve a high-quality concrete surface finish on exposed columns without any additional “post-strike” improvement work.
Coordination between the various sub-contractors was key to the success of the project. Stephenson had to receive work areas from the groundworker and in turn had to hand areas back to various other sub-contractors, one example being the glulam installers who required that the concrete works be finished to a very high level of accuracy and very small tolerances.
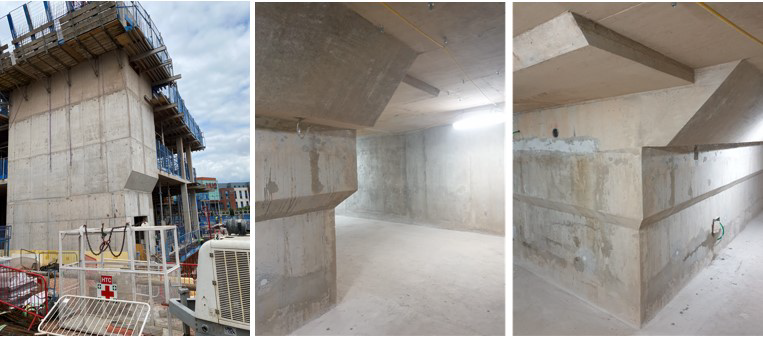
Exceeding the Client’s expectations
The main works were completed in October 2020 which was principally due to the impacts of COVID 19 which caused several weeks of delay due to a total site shut-down followed by additional protective measures when site eventually re-opened.
Since completion of the project Stephenson have secured new projects with Kier which in part can be viewed as legacy to the success achieved on the complex St Sidwells project and also as testimony to the teamwork which delivered this landmark facility.
Repeatability
This project was a distinctive building form but using predominantly traditional elements and materials and as such many of the techniques employed were derivative of our typical working practices with critical emphasis on the sequence and interconnectivity of elements.
It is unlikely that such an expansive array of non-typical details and design forms would be encountered on a single project but it definitely has provided focus on the importance of completing a catholic pre-construction design and build review and ensuring that a fully integrated delivery solution is established in co-ordination with our Clients and the Design Team.
R&D / Use of Technology
The confidence pool posed a challenge to traditional insitu cast concrete as the pool edges were both curved and sloping as well as the soffit of the whole pool falling in one direction.
In addition there was a bullnose “deck drain” channel to the inside of the pool which followed the pools curved edge profile. The 3D model of the channel was sent to Cordek who then produced a GRP shutter to form the bullnose drainage channel. This was then fixed down to the sloping timber deck and concrete poured.
This small area was suspended over the pool plant room and in order to achieve the design loadings the rebar was made up of 32mm diameter bars top and bottom requiring 35 tonnes of rebar in a slab area no bigger than 10m x 10m which might normally contain less than half that quantity.
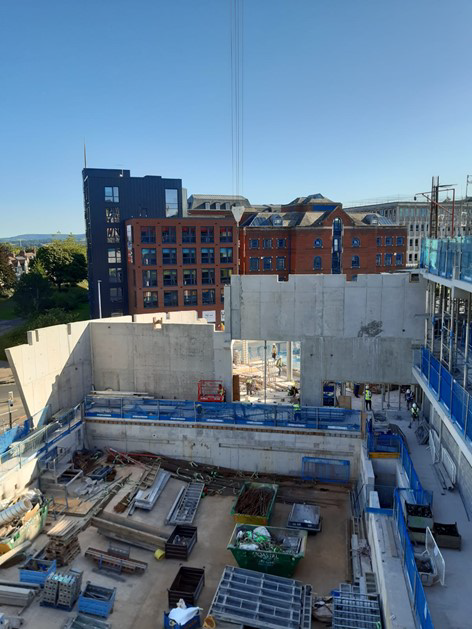


Sustainability
Being a Passivhaus project the reduction of embodied energy was a crucial part of the procurement strategy as we were challenged to make our contribution to the project performance objectives.
Stephenson rigorously pursued all available opportunities to plan and execute waste reduction and responsible sourcing strategies in order to support the wider project objectives.

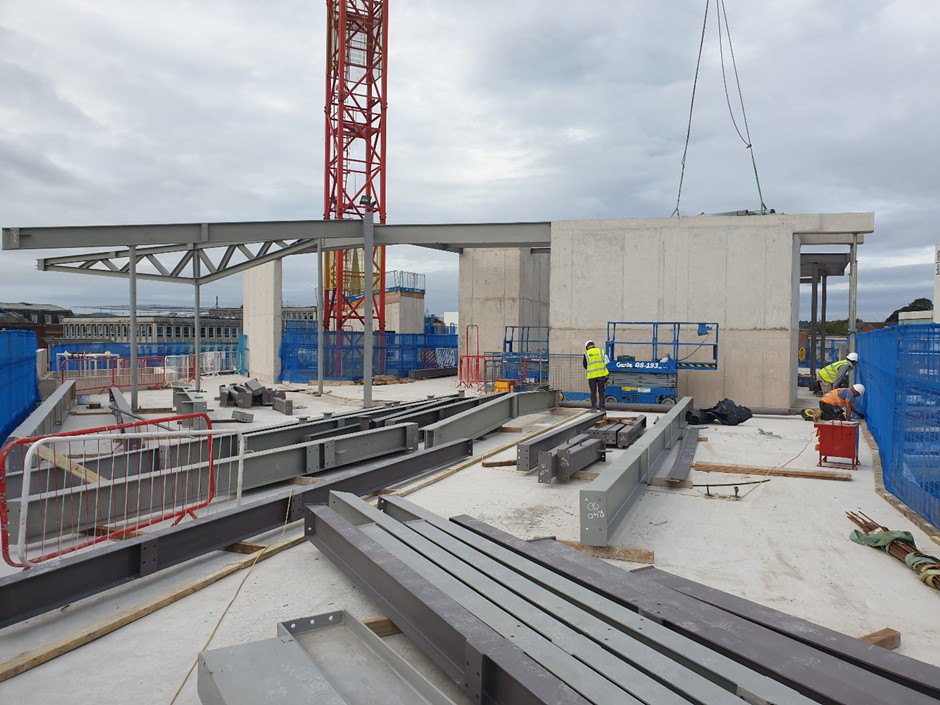
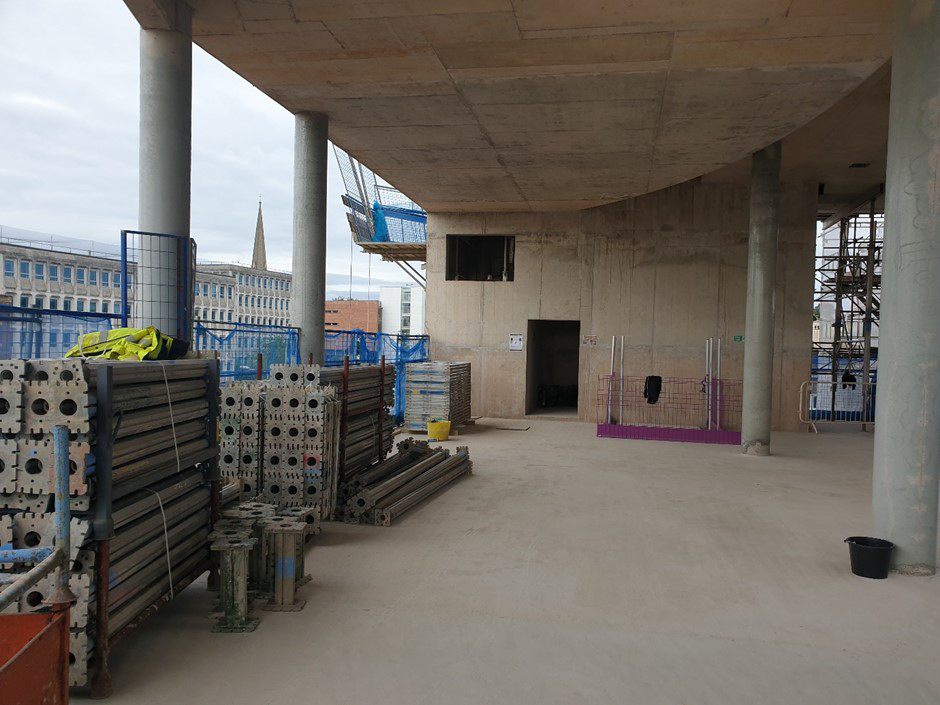
Comments